AIR COOLED AFTERCOOLERS
An air-cooled aftercoolers is a device used in industrial systems and HVAC equipment to cool air after it has been compressed. It is typically used in conjunction with an air compressor to reduce the temperature of compressed air and ensure that the air does not become too hot. The aftercooler achieves this by passing the compressed air through a finned chamber. The air is then cooled by ambient air passing across the fins, as well as by external cooling fans. After the air has been cooled, it is ready for use in the system.
Air-cooled aftercoolers typically feature a bolted cover and an internal core composed of aluminum finned tubes. The finned tubes heat up as the compressed air passes through them, and then cool down as ambient air passes over them. The external fans help to accelerate the cooling process by forcing air onto the finned tubes. The air-cooled aftercooler is efficient and reliable, as it requires minimal maintenance and operates without the need of additional cooling fluids.
The air-cooled aftercooler is an invaluable device in any industrial process, providing a cost-effective method of cooling compressed air without the need for complex and bulky systems. It can help to reduce long-term energy costs and ensure that systems remain safe, reliable and efficient. Understanding the operation and maintenance of an air-cooled aftercooler is essential for running a successful business and ensuring that processes run smoothly.
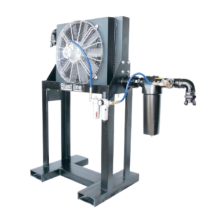
Air Compressor Horsepower (hp) | Internal Airflow Maximum CFM | Recommended BL Series Model No. |
25 – 50 HP | 245 | BL 200 |
25 – 75 HP | 539 | BL 450 |
100 – 125 HP | 785 | BL 600 |
150 – 200 HP | 1569 | BL 1000 |
225 – 350 HP | 2300 | BL 1600 |
jfj jhdjkfj kdkkdj jdjfdska jddkj kjfdkd kskqowejf iweoej iwef ieoesjdoe eooe eooejfjnip jldh iorji ioejf iohweo ojh roho
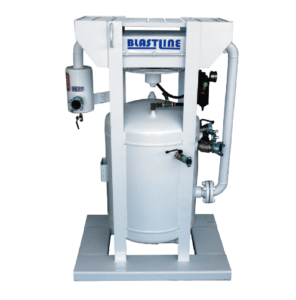
Maximum Working Pressure | 250 psi |
Cooler | Aluminum |
Shroud | Powder Painted Steel |
Fan Guard | Zinc Plated Steel |
Fan Blade | Polypropylene Blades |
A cooler/Separator is required to reduce the temperatures and discharge the condensed moisture. By using this Blast pack System increases production and reduces downtime and maintenance cost. Moisture in the compressed air system contaminates both controls and abrasive causing the abrasive to bridge and not flow properly. This system effectively provide cooler, cleaner and dry air to your blast pots with negligible drop in pressure. Two system types are available to meet your specific requirements after coolers and air dryers and air dryers.
This system effectively provide cooler, cleaner and dry air to your blast pots with negligible drop in pressure. Two system types are available to meet your specific requirements after coolers and air dryers.